Surrounding & Controlling Underground Leaks
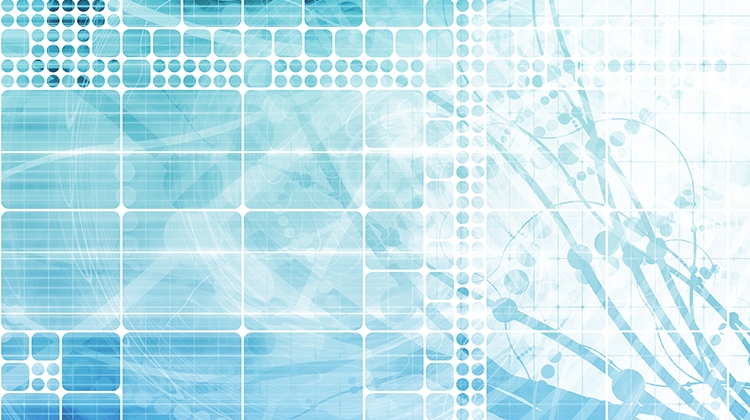
Double-wall containment: an answer to unsafe piping systems
While most in the pharmaceutical industry understand the need for double-wall containment piping systems, our field observations indicate that many companies do not. We frequently see pipes that should be (but are not) double-wall containment systems. This article presents an overview of the topic, so that readers who may not know they have a problem might be motivated to have their piping system upgraded. We also discuss risk management as a multifaceted, nonlinear process to further illustrate the risks of not having a containment system in place.
Leaks cannot always be prevented, but they can be contained. Because leaks in underground fluid pipes can take years to make themselves known, the choices and expenses of containing a toxic, corrosive, and/or hazardous leak present a challenge to decision-makers, especially in the pharmaceutical field, where leaks can pose especially deleterious threats to public health and require urgent solutions.
For underground fluid-transferring systems, one of the best ways to achieve peace of mind and ensure compliance with the US Environmental Protection Agency (EPA), Resource Conservation and Recovery Act, and other guidelines is to use double-wall containment piping systems. EPA regulations1 ,2 ,3 mandate that underground transportation of hazardous materials must be protected from release into the environment.
- 1US Environmental Protection Agency. “Resource Conservation and Recovery Act (RCRA) Overview.” https://www.epa.gov/rcra/resource-conservation-and-recovery-act-rcra-overview
- 2Federal Register 80, no. 135. Part II: Environmental Protection Agency. “40 CFR Parts 280 and 281: Revising Underground Storage Tank Regulations.” 15 July 2015. https://www.gpo.gov/fdsys/pkg/FR-2015-07-15/pdf/2015-15914.pdf
- 3US Environmental Protection Agency. “Health and Environmental Agencies of US States and Territories.” https://www.epa.gov/home/health-and-environmental-agencies-us-states-and-territories
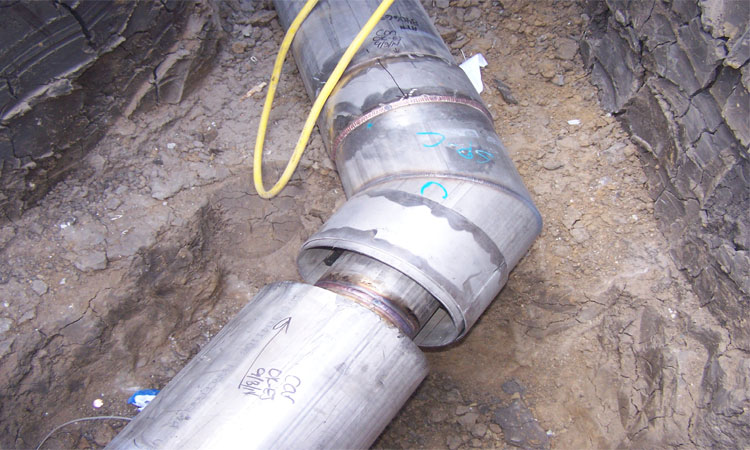
Design Considerations
Whether installing a new double-wall containment piping system or altering an existing system, there are several design considerations to address, including pipe materials, fluid temperature and pressure, leak-detection methods, inspection, and testing requirements.
Pipe materials
Double-wall containment pipe is designed as its name suggests. The choice of material for both the carrier or product (inner) pipe and the containment (outer) pipe material depends on the liquid type, temperature, pressure, and corrosive properties. Polypropylene can be the least expensive; stainless steel can be among the most expensive. Fiberglass-reinforced plastic (FRP) pipe is lightweight and strong, and provides a good return on investment for the proper circumstances. Table A compares representative pipe materials and applications.
What the table does not convey are the many choices and tradeoffs available for specific combinations of chemicals, media and fluid temperatures, as well as fluid pressures and system materials, including combinations of carrier and containment pipes with and without internal and external coatings. Neither does it represent all the questions of installation, safety, costs, and ease of use or maintenance. The final cost of the system, including pipe materials, leak detection system, design fees, installation, testing, commissioning, and documentation may have less to do with the pipe materials themselves than with the final configuration necessary to make sure the fluid leak can be contained.
Installation
Installation time ranges from almost immediate “plug and play” quick socket fusion to multiple hours of on-site welding, depending on the system. When installing a pipe system, it is important to plan for and include leak-detection, inspection, and pressure-testing procedures. The keys to making the right decisions and lowering project risk are: 1) choosing a well-designed system as specified by an experienced engineer; 2) following manufacturer procedures; and 3) using trained installers.
Leak detection
The automatic leak-detection and reporting system can be located between the inner and outer pipe and at the lowest point of the system. Leaks can also be detected and observed through multiple inspection ports located at the lowest level of the pipe system or at a collection double-containment sump. Because electronic systems can fail, to be truly proactive and safe any system design should include frequent visual inspections for leaks as mandated by toxic substance control regulations.
Inspection and pressure testing
A complete visual pipe inspection for both carrier and containment systems should be performed before pressure testing, including welds, joints, cracks, and slopes. Once the visual inspection has been completed, a pressure test can be conducted as follows:
CARRIER PIPE
Once the carrier pipe is installed, it is essential to certify the pipe and to confirm that it can handle the design pressure. For a gravity-flow system, most plumbing codes require a 1/8 inch per foot slope and a working head pressure test for 15 minutes. Other systems may require that the system be certified at a higher pressure rating; this will allow more flexibility for future pipe inspections with higher-pressure media, especially when a suspected leak cannot be located with a borescope. Choosing the correct pipe material will determine the system’s ability to handle higher pressure testing.
CONTAINMENT PIPE
When the carrier pipe has passed both the pressure test and an inspection by a certified professional, the containment pipe can be closed and tested. Usually, this requires a lower pressure rating test than the carrier pipe. In some systems, the containment pipe is tested when the carrier pipe is charged.
In general, inspections and testing can be progressive or sectional. This is determined at various project phases.
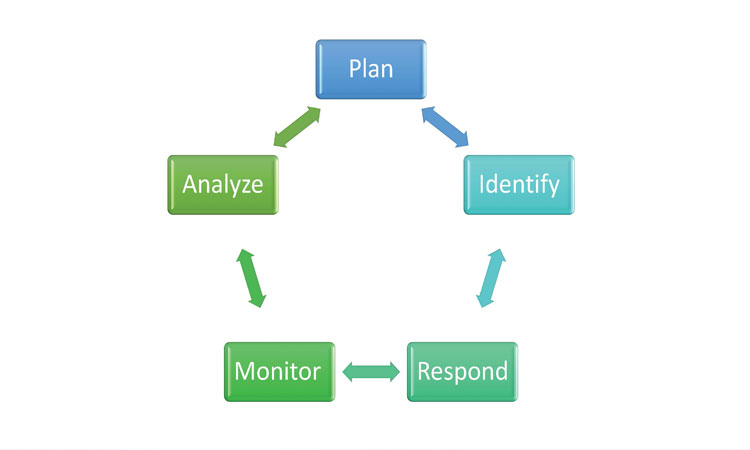
Underground or Aboveground?
Underground and aboveground containment piping systems both have pros and cons.
Underground
Pro: In some applications, underground fluid-transfer systems rely on gravity flow, avoiding pump and installation costs.
Con: Underground double-walled containment piping in an elongated system can hide a slow leak for a long time before it finds its way to the end or lowest point of the piping system. Pinpointing a particularly small leak’s location can be a challenge, especially when it’s not detectable via a borescope inspection. Additionally, false alarms can occur when an automatic leak-detection system can’t differentiate between a dangerous toxic leak and harmless condensation between the inner and outer pipes. Frequent manual inspection and testing can preclude these false readings, averting unnecessary stress and expense.
Aboveground
Pro: Aboveground systems make leak detection simpler, if only because manual observation is straightforward. An inspection leg with a sampling port can be added to the pipe system to collect fluid leaking from the containment system. Additionally, the containment pipe in a polypropylene system can be clear polypropylene; stainless steel pipe can include a dead leg to check for carrier pipe leaks.
Con: A toxic leak in an aboveground system—especially above a building complex—can enter the public water system through a roof drain or site water runoff. Precautions such as a secondary containment pipe or containment pit may be required to prevent accidental damage to the physical plant and mitigate danger to employees.
Risk-Management Process
Piping system selection is subject to space restrictions, fluid pressure, installation, fittings, documentation requirements, susceptibility to cracking—and, of course, cost. There is no one-size-fits-all solution. It is important, therefore, to identify risks and incorporate an overall risk-control methodology.
Surrounding and controlling toxic underground leaks hinges on a commitment to risk management. Risk management is not linear in its execution. It is a multifaceted process that requires simultaneous attention to identifying, analyzing, monitoring, planning, and responding. This may be a difficult position to accept, but we believe it is important.
Negligence and ignorance are expensive, not only in monetary fines that can run into millions of dollars, but more importantly in health problems, employee or community medical costs, equipment damage, lost production, rebuilding costs, environmental issues, and damage to the organization’s reputation.
Compliance decisions rendered against companies will be based on variables that include the fluids’ corrosive or hazardous properties, temperature, and conformance to codes such as ASME Process Piping Standard B31.3
Selecting the proper materials is an important step. Stainless steel piping and fittings are among the most expensive of the products listed above, but they may be the only options that will contain leaks when operating and testing a pipe under high pressure. Polypropylene or FRP might work for now. But because new materials and science are continually advancing, an annual system review—at a minimum—is prudent. Quarterly and monthly evaluations are recommended. Daily inspection and system evaluation is the best defense against failures.
Conclusion
Today’s marketplace demands responsibility and responsiveness, but the world’s need for proactive attention to containing and preventing toxic leaks cannot be overlooked. Double-wall containment piping systems, when correctly researched, properly installed, and professionally attended will help avert crises, injury, disease, and death. Component choices can be compared objectively with the help of designers and experts, and then certified by a professional engineer before the project is submitted to the appropriate governmental entity for approval.4 ,5 https://www.ecfr.gov
The pharmaceutical industry is fortunate to have an abundance of engineers, suppliers, and designers to discover the best, most effective, lowest risk double-walled containment systems for surrounding and controlling underground toxic pipe leaks.
Manufacturer | A | B | C |
---|---|---|---|
Material: carrier and containment pipe |
Polypropylene | FRP | Stainless steel T316L |
Applications |
|
|
|
Maximum temperature (°F) | 160 | 160 | 170 |
Carrier pipe diameter (inches) | 1–16 | 1–12 | 0.5–20 |
Containment pipe diameter (inches) |
3–20 | 3–16 | 2–26 |
Internal corrosive coating | None | Epoxy | None |
External corrosive coating | None | Epoxy | None |
Wall thickness (inches) | 0.280 for 6⨯8 inch | 0.170 for 4–6 inch 0.220 for 10–14 inch |
0.28 for 6 inch 0.365 for 10 inch (schedule 40 pipe size) |
- 3
- 4US Code of Federal Regulations. Title 40, Part 280. “Technical Standards and Corrective Action Requirements for Owners and Operators of Underground Storage Tanks (UST).” https://www.ecfr.gov
- 5US Code of Federal Regulations. Title 40, Part 281. “Approval of State Underground Storage Tank Program.”