Sustainability: Where Is LEED Leading Us?

In 2000, the U.S. Green Building Council (USGBC) introduced Leadership in Energy and Environmental Design (LEED) to create a methodology to promote sustainability-focused practices in the building industry. This article reviews the earliest protype that we know of for a LEED manufacturing facility, presents a real-world case study of a pharmaceutical manufacturing facility achieving LEED Gold, and describes sustainability certifications that go beyond LEED.
Since the first LEED project, there have been more than 90,000 LEED-certified projects across more than 162 countries. More than 2.2 million square feet of construction are LEED certified every day.1 According to USGBC, LEED “is the most widely used green building rating system in the world. Available for virtually all building, community and home project types, LEED provides a framework to create healthy, highly efficient and cost-saving green buildings. LEED certification is a globally recognized symbol of sustainability achievement.”2
Prototype LEED Manufacturing Facility
Jim Dolceamore, PE, from AstraZeneca (retired), a former ISPE Board Member and past president of the Delaware Valley Chapter, was an early proponent of utilizing LEED facility design. With him, we decided to propose a session on the topic for the 2006 ISPE Annual Meeting in Orlando, Florida. At that time, LEED was in its early phase. Only 5,000 projects had been registered by the USGBC, with 716 certified, and there had been very few, if any, LEED-certified cGMP manufacturing facilities built anywhere in the world. Because we could not identify any pharmaceutical manufacturing LEED-certified facilities at that time, we decided to create a prototype cGMP solid dose manufacturing facility, to score the facility, and to summarize our findings. Bernie Friel, past President of Genesis Engineering and an early ISPE member, joined our team to lead the mechanical, electrical, and plumbing (MEP) engineering portion. Our goal was to push our industry forward toward sustainability by demonstrating that LEED was a feasible and economical option for a pharmaceutical manufacturing facility.
Prototype Outline and Parameters
The following is the outline of our prototype:
The protype project is called Greentech Pharma and is a 131,000 cGMP solid dose manufacturing facility. The program includes shipping/receiving, warehouse, manufacturing, administration, QC/QA laboratory, packaging and support functions. Since we had the option of where to locate our project, we chose a site near public transportation, as this we knew is a LEED goal and we also know this is not usual for a pharmaceutical manufacturing facility.… The site was shown on a 25 acre site.
The facility is organized around a central utility spine that separates the API facility from the finishing facility and allows for the future doubling of the facility size on the site. An 8-foot-high perimeter wall will enclose the site.
To understand how to achieve LEED, we had to model our prototype facility’s utilities, as these are critical to the design. Note that LEED did not acknowledge process energy at the time. Table 1 presents the parameters that we developed based on the program and typical air classifications.
Area Location | Area, sq ft | Height | Lights w/SF | Power W/SF | Room Temp,°F | Relative humidity, %ISO Class | Minimum AC/H | ISO Class | % OA | |
---|---|---|---|---|---|---|---|---|---|---|
Min. | Max | |||||||||
Manufacturing | ||||||||||
GMP Class 100,000 | 12,000 | 12 | 2.1 | 10 | 68 | 30 | 50 | 20 | 8 | 30 |
GMP Class 10,000 | 6,000 | 12 | 2.1 | 10 | 68 | 30 | 50 | 40 | 7 | 50 |
QC lab | 5,000 | 9 | 1.4 | 10 | 68 | 30 | 50 | 10 | 100 | |
Locker rooms | 2,500 | 9 | 0.9 | 75 | 6 | 100 | ||||
Subtotal | 25,500 | |||||||||
Packaging | ||||||||||
Primary | 5,000 | 16 | 2.1 | 5 | 72 | 30 | 50 | 10 | 20 | |
Secondary | 10,000 | 16 | 2.1 | 5 | 72 | 30 | 50 | 10 | 20 | |
Support areas | 3,700 | 16 | 1.2 | 2 | 72 | 30 | 50 | 10 | ||
Subtotal | 18,700 | |||||||||
Warehouse | ||||||||||
Ambient storage | 24,000 | 35 | 0.9 | 72.5 | 20 | 50 | 3 | 10 | ||
4°C storage | 2,500 | 18 | 1.4 | |||||||
–20°C storage | 500 | 12 | 1.4 | |||||||
Acid/base storage | 1,500 | 24 | 0.9 | 75 | 20 | 50 | 4 | 100 | ||
Flammable storage | 1,500 | 24 | 0.9 | 75 | 20 | 50 | 4 | 100 | ||
Subtotal | 30,000 | |||||||||
Shipping/receiving | 7,500 | 20 | 0.9 | 75 | 10 | |||||
Administration | ||||||||||
Offices | 18,500 | 9 | 1.1 | 2 | 75 | 50 | 10 | |||
Circulation | 2,500 | 9 | 0.5 | 0 | 75 | 50 | 10 | |||
Break room | 5,000 | 9 | 0.9 | 0 | 75 | 50 | 10 | |||
Server room | 1,000 | 9 | 1.1 | 80 | 72 | 40 | 50 | 10 | ||
Training room | 5,000 | 9 | 1.4 | 10 | 72 | 50 | 10 | |||
Subtotal | 32,000 | |||||||||
Central utility building | ||||||||||
Maintenance support | 2,500 | 20 | 1.9 | 10 | 75 | 10 | ||||
Mechanics and electrical space | 6,500 | 20 | 1.5 | 90 | ||||||
Subtotal | 9,000 | |||||||||
Waste solvent storage | 1,500 | 12 | 1.4 | 90 | 12 | 100 | ||||
Connecting corridor | 7,000 | 10 | 0.5 | 75 | 10 | |||||
TOTAL | 131,200 |
Scoring
We treated this prototype as a real project and proceeded to score the project to see if we could achieve certification. Table 2 depicts the division of points available for LEED certification at that time.
Level | No. of Points |
Certified | 26-32 |
Silver | 33-38 |
Gold | 38-51 |
Platinum | ≥52 |
Table 3 and the following subsections capture how we achieved LEED certification.
Sustainable Sites: 7 Points Achieved (14 Points Maximum)
The prerequisite was erosion control. This was easy to achieve. The seven points were achieved through the following actions:
- We did not develop prime farmland. Notably, historically many new plants may be in these types of areas. Avoiding rural development is a good goal for future projects.
- We located the building within ½ mile of existing transportation. How many plants can achieve this? Again, this is a good goal for future projects.
- We provided a bicycle and changing room. This was very easy to achieve.
- We stayed within the zoning code parking requirements. The point of this was to not overbuild the parking. This is a good guideline for any project. Most local zoning boards will allow you to build what you need, and to not overbuild, if you “bank” the remaining spaces. This is a more sustainable approach, and a good guide for future projects.
- We allocated 5% of parking spaces for fuel-efficient vehicles.
- We used highly reflective roofing for our region.
- We controlled light pollution for exterior lighting.
Water Efficiency: 2 Points Achieved (5 Points Maximum)
There was no prerequisite. We scored the points by:
- Reducing potable water use, excluding process water, by 50%
- Using energy-efficient landscaping.
Energy and Atmosphere: 4 Points Achieved (17 Points Maximum)
The first prerequisite was fundamental building commissioning. For pharma projects, this is typically easy to achieve. The second prerequisite was minimum energy performance, and the final prerequisite was fundamental refrigerant management. We achieved points for:
- Enhanced commissioning
- Enhanced refrigerant management
- Purchasing Green power (35%)
- Measurement and verification
Materials and Resources: 4 Points Achieved (13 Points Maximum)
The prerequisite was storage and collection of recyclables. The following efforts earned points:
- Construction waste management: diverting 50% from disposal
- Construction waste management: diverting 75% from landfill
- Using 10% regional materials
- Using certified wood
Indoor Environmental Quality (IEQ): 14 Points Achieved (17 Points Maximum)
The prerequisites were minimum indoor air quality performance and environmental tobacco smoke control. We earned points for:
- Outdoor air delivery monitoring
- Increased ventilation
- Construction IEQ management plan during construction
- Construction IEQ management plan before occupancy
- Low-emitting materials: adhesives and sealants
- Low-emitting materials: paints and coatings
- Low-emitting materials: carpet systems
- Low-emitting materials: agricultural and wood products
- Indoor chemical and pollutant source control
- Controllability of lighting for 90% of occupants. We assumed this in offices.
- Thermal comfort for design, according to American Society of Heating, Refrigerating and Air-Conditioning Engineers (ASHRAE) Standard 55
- Survey of thermal comfort
- Daylight and views: 75% of spaces
- Daylight and views: 90% of occupied spaces
Innovation: 2 Points Achieved (5 Points Maximum)
There was no prerequisite for this area. We achieved points by:
- Involving a LEED-accredited professional
- Making industry change its practices for air changes
Area | Achieved | Max Possible |
---|---|---|
Sustainable sites | 7 | 14 |
Water efficiency | 2 | 5 |
Energy and atmosphere | 4 | 17 |
Materials and resources | 4 | 13 |
Indoor environmental quality | 14 | 17 |
Innovation and design process | 2 | 5 |
Total | 37 | 71 |
Project Impact
Because this was a new venture, we tried to estimate how LEED-certifying the project would affect the owner. Anticipating that design costs would increase, the owner would have higher level of participation, and we might need specialty consultants, we forecast a 3%–5% increase in construction costs. We calculated the additional design cost at $75,000 at that time, or approximately 0.01% of a $40 million construction cost. For benefits, we outlined operational savings, maintenance improvements due to better documentation, possible higher employee productivity due to better indoor air quality and natural light, and the public relations opportunity to market the owner as a good citizen doing the right thing.
During this study, we also noted areas where the USGBC could change, clarify, or add incentives to better target manufacturing projects, including the following:
- Heat recovery/energy efficiency for manufacturing processes
- Is process water exempt from water requirements?
- Photovoltaic encouragement
- Setbacks on cleanrooms during unoccupied times
- Lighting control
- Wind wake analysis—add as an innovation point
- Daylight—is this a good point for manufacturing?
- Building efficiency—net/gross building volume and orientation
- Achieving 10.5% energy reduction is difficult–could process loads be excluded?
- Why increase ventilation when it increases energy use?
Case Study: McNeil Consumer Healthcare Manufacturing Facility
Having certified our imaginary facility, we had the opportunity to seek LEED Gold certification for a real project in 2010: the complete renovation of the McNeil Consumer Healthcare manufacturing facility in Fort Washington, Pennsylvania. A goal of the project from the beginning, as stressed by Phil Rudio, Global Director of Engineering and Design at Johnson and Johnson (J&J), was LEED Gold status:
J&J’s core operating principles are engrained in our credo, which states that “We are responsible to the communities in which we live and work and to the world community as well.”
J&J’s Sustainability Policy requires us to achieve LEED certification on all new buildings. This is well aligned with our commitment to the communities by constructing energy-efficient, environmentally sound facilities.
Project Goals and Challenges
The Fort Washington facility was a cGMP pharmaceutical manufacturing facility with a total building area of 500,000 sq ft. The project had an accelerated schedule to meet renovation goals. Among those goals was to attain LEED Gold certification for 346,000 sq ft (approximately 70% of the total building area), including:
- Production
- Packaging
- Warehouse
- Microbiology laboratory
- Amenities (cafeteria, lockers, Restrooms)
Unlike our prototype, in which we started design and construction from scratch, this project was set on an existing site with existing buildings, including existing facilities for R&D, pilot plant, QA labs, micro-labs, manufacturing, and warehouse. These real-world factors presented new challenges: Some of the existing facilities were to remain unchanged and therefore could not be included in the LEED project boundary. Also, utilities serving these existing facilities need to remain in operation and would not change.
A key decision was selecting the rating system to use for the project. We chose the LEED Commercial Interior (CI) rating system(see Table 4) because it best matched the description of the project. Thirty credits are unique to the CI rating system, and project team determined CI to be especially advantageous in the Energy and Atmosphere (E&A) division because 22 points can be earned without energy modeling (more points with less time equals savings for the client).
Level | No. of Points |
Certified | 40-49 |
Silver | 50-59 |
Gold | 60-79 |
Platinum | ≥80 |
The LEED submission type was a split review. The first review allowed an early sense of how many design credits could be anticipated. If the number of credits were insufficient, the team would have an opportunity to revise its design and construction plan before the construction submission review.
The project succeeded in achieving LEED Gold. Figure 1 shows the credits earned (green) and maximum possible (blue) credits.
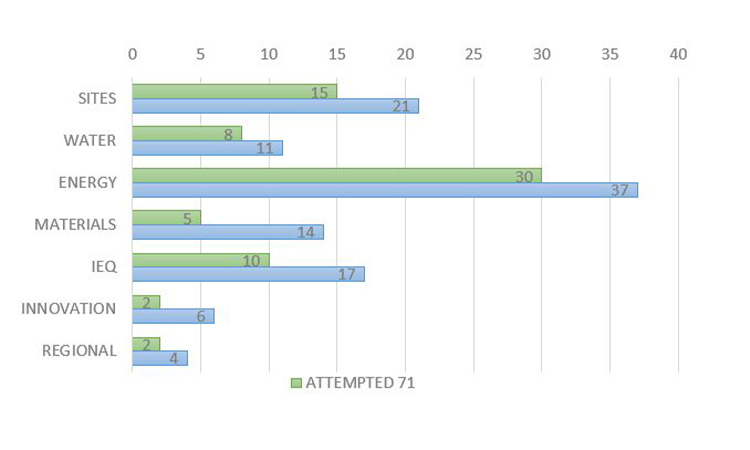
The following is a summary of how we attained these points:
- Sustainable Sites:
- SSc1 Site Selection, Option 2—Locate tenant space in a building that has in place one or more of certain characteristics: Here, our strategy was to select the LEED rating system that most clearly fit the project.
- PATH 5 Heat Island Effect—Roof: This effort earned 1 point plus a Regional Priority Point.
- PATH 7 and 8 Water Efficient Landscaping: No irrigation was provided on the site (4 points).
- SSc3.3 Alternative Transportation—Bicycle Storage and Changing Rooms: We provided bicycle racks for 5.87% of occupants and shower facilities for 2.57% of occupants (2 points).
- SSc3.3 Alternative Transportation—Parking Availability: We earned 2 points plus an additional Regional Priority Point by providing reserved carpool/van-pool parking spaces for at least 5% of the building occupants and removing 11 existing parking spaces.
- Water Reduction: WEc1 Water Use Reduction: The use of dual flush toilets, low-flush urinals, low-flow showers and kitchen sinks earned 8 points.
- Energy and Atmosphere:
- EAc1.1 Optimize Energy Performance—Lighting Power: We earned 5 points for reducing energy use by 35%. Because the site is a manufacturing facility, the number of watts per square foot allowed by ASHRAE and International Energy Conservation Code (IECC) codes increases to 1.3. Also, the warehouse and shell space included in LEED project boundary, require a lower foot-candle level per the owner’s lighting standards. We used high-bay T5HO fixtures to achieve the most efficient lighting for these spaces, which reduced the amount of lighting power needed for the building. We used the Building Method to calculate lighting power density, rather than the space-by-space method; with the latter method, we would have met difficulty with the White and Grey spaces that required 70 foot-candles per the owner standard.
- EAc1.2 Optimize Energy Performance—Lighting Controls: We earned 1 point by installing daylight-responsive controls in 100% of occupied spaces within 15 feet of windows.
- EAc1.3 Optimize Energy Performance—HVAC: Using a prescriptive method achieved 5 points. Strategies included equipment efficiency, appropriate zoning, and controls.
- EAc1.4 Optimize Energy Performance—Equipment and Appliances: We earned 4 points because all new equipment and appliances are energy-star rated (96.5% of all equipment and appliances are by rated power).
- EAc3 Measurement and Verification: Utilities are separately submitted, with 5 points earned.
- Materials and Resources:
- MRc1.1 Tenant Space Long-Term Commitment: We earned 1 point.
- MRc2 Construction Waste Management: Diverting from disposal a minimum of 75% of construction debris was worth 2 points. Our goal was to get an exemplary performance of 95% of diverted material.
- MRc3.2 Material Reuse Furniture and Furnishings. We earned 1 point because all workstations, office and conference room furniture, and computer carrels are reused.
- MRc4 Recycled Content: We achieved 1 point by using specified materials with high recycled content.
- MRc7 Certified Wood: We earned 1 point for specified wood that is Forest Stewardship Council (FSC) certified.
- IEQ:
- IEQc2 Increased Ventilation—Case 1 for mechanically ventilated spaces: We earned 1 point by increasing outdoor air ventilation rates to all occupied spaces by at least 30% above the minimum rates required by ASHRAE 62.1-2007.
- IEQc3.1 Construction IAQ Management Plan During Construction: Protecting materials from moisture damage and using filters on air handlers used during construction earned 1 point.
- IEQc3.2 Construction IAQ Management Plan Before Occupancy–Option 1: Conducting a flush out earned 1 point.
- IEQc4.1 Low-Emitting Materials—Adhesives and Sealants: The use of specified adhesives, sealants and sealant primers complying with South Coast Air Quality Management District (SCAQMD) Rule 1168 resulted in 1 point.
- IEQc4.2 Low-Emitting Materials—Paints and Coatings: Because a conductive primer exceeded allowable VOC levels, we used the volatile organic compound (VOC) budget method and earned 1 point.
- IEQc4.3 Low-Emitting Materials—Flooring Systems. All carpet is certified by the Carpet and Rug Institute (CRI); hard surface flooring is FloorScore certified, and carpet adhesive has less than 50 g VOC per liter. These choices earned 1 point.
- IEQc4.4 Low-Emitting Materials—Composite Wood and Agrifiber Product. The use of specified materials that do not contain added urea-formaldehyde resins resulted in 1 point.
- IEQc4.5 Low-Emitting Materials—Systems Furniture and Seating: The use of Greenguard-certified furniture was worth 1 point.
- IEQc7.1 Thermal Comfort—Design: We earned 1 point because HVAC systems are designed to meet requirements of ASHRAE Standard 55-2004.
- IEQc7.2 Thermal Comfort—Verification: We earned 1 point for promising to implement a survey and take corrective action if more than 20% of occupants are dissatisfied with thermal comfort.
- Innovation in Design: We achieved 1 point for diverting more than 95 % of the construction waste.
USGBC denied several points that we hoped to earn on the project. One of these was for certified wood, because the contractor did not have the proper chain of custody number on the materials submittal form.
Overall Project Impact
Additional time was spent on documentation and coordination meetings between the design team, the owner and Turner Construction, the construction manager for the project. The fees related to LEED were approximately $80,000, and the overall construction budget did not increase, due to the high sustainability standards of J&J.
Alternatives to LEED Certification
Since the McNeil renovation project, we have participated in many other LEED projects for pharmaceutical manufacturing facilities. The ISPE Facility of the Year Awards (FOYA) program, which was started in 2004, created a category for sustainability, which has generated multiple innovative projects.3
Based on anecdotal information, we believe that many companies are implementing their own sustainability standards and using the LEED checklist, even if they are not pursuing official certification. Building codes such as IECC 2018 have also been increasing their sustainability requirements, clarifying that, regardless of design methodology, system commissioning is required.
Although LEED offers a proven framework for projects to incorporate sustainable design into many aspects of a project, two certification systems that go beyond LEED are options for owners and project teams that want to achieve higher levels of sustainable design. Core Green Building Certification4 and Living Building Challenge (LBC) Version 4.0 [5] are both managed by the International Living Future Institute (ILFI). Core is the first step up beyond the LEED certification system, and LBC is the most rigorous certification currently available on the market. Projects that meet the requirements for Full Living Certified status using LBC have achieved the highest levels of holistic sustainable design.
Core Green Building Certification, which uses the same framework as LBC, identifies the 10 best LBC practices that a project must meet to be considered a sustainable building and achieve CORE certification:
- Ecology of place
- Human-scaled living
- Responsible water use
- Energy and carbon reduction
- Healthy interior environment
- Responsible materials
- Universal access
- inclusion
- Beauty and biophilia
- Education and inspiration
According to ILFI, Core “seeks to rapidly diminish the gap between the highest level of established green building certification programs and the aspiration of the Living Building Challenge. Projects that achieve CORE certification can claim to be role models in their communities for redefining the future of the building environment.”4 Core certification can be used for new construction, existing buildings, or interior renovations of multi-family, commercial, institutional, and medical/laboratory type projects.
Core certification is based on actual performance. A project must be operating for a minimum of 12 months prior to the audit to verify that all requirements have been met. To learn more about Core, see reference 4.
LBC Version 4.0 was released in 2019. It asks, “What does good look like?” ILFI states:
LBC 4.0 focuses on the relationship between impact and effort. While LBC 4.0 continues the standard’s mission of visionary, but attainable building goals, it also recognizes that not all projects face the same challenges or share in the same opportunities. Regenerative design should be attainable to everyone, everywhere. With 4.0, we are creating a streamlined approach focused on maximizing positive impacts specific to the place, community, and culture of the project. This revised version of the Living Building Challenge has been developed based on two goals: to simplify the program so the level of effort of teams is better aligned with their impacts, at both project and market scales; and to fill the gap between the highest levels of mainstream green building certifications, and the entry point to the Living Building Challenge. LBC 4.0 also raises the bar by requiring that teams address basic issues in all petals, even if the project is primarily focused on a more limited scope of priorities.”5
LBC is organized into seven performance categories, or “Petals”: Place, Water, Energy, Health and Happiness, Materials, Equity, and Beauty. The Petals are then further broken down into 20 imperatives. Different imperatives apply to different “typologies” (project types), including new buildings, existing buildings, interiors, landscape, and infrastructure. As with CORE, an audit of actual performance is used to determine whether projects meet the requirements of the imperatives, and a project must be operating for a minimum of 12 months prior to the audit. LBC offers two pathways to certification: Petal certification and Living certification. For Petal certifications, all of the CORE imperatives and the remaining imperatives within the Water, Energy, or Materials Petal are required. Living certification requires achieving all of the imperative assigned to the project typology. For new buildings, all 20 imperatives must be achieved.
In 2019, LBC marked another milestone, with over 100 certified buildings and over 500 registered projects trying to meet the challenge.5 To learn more about the Living Building Challenge, see reference 5.