Cold Systems as a Solution to Decarbonize Water Purification

The biotechnology and pharmaceutical sectors have pledged to reduce greenhouse gas (GHG) emissions as the climate concerns of consumers, investors, and regulators continue to grow. In seeking to benefit from this demand for sustainability and the potential for cost-saving opportunities, life science product manufacturers have started to evaluate the climate impact of their own labs and production facilities. This in-depth examination of the sectors’ direct manufacturing processes uncovered one of the largest carbon emitters: water for injection (WFI).
Decarbonizing WFI
A growing number of manufacturers have pledged to reduce these emissions through a commitment to achieving “net-zero,” a state in which the GHGs entering the atmosphere is balanced by their removal from the atmosphere. Others are pioneering corporate initiatives to advance carbon neutrality ambitions well beyond emission sequestration and neutralization to eventually become fossil-fuel free. In either case, the achievement of these targets on time and on budget is based on the timely deployment of cost-effective energy efficiency and renewable energy projects. Crucially, WFI decarbonization is one of such interventions. Switching from hot to cold WFI systems converts the associated energy consumption from fossil-fired heat to electricity potentially powered by renewable sources, eliminating onsite combustion emissions and keeping the industry compliant with regulations and its own commitments to a net-zero future.
Background on Carbon Emissions
The biotechnology and pharmaceutical industry, which is ranked high among the world’s largest carbon emitters and is responsible for 197 tonnes of carbon dioxide equivalent (tCO2e), presently ranks 15th on the list of highest emitters, outpacing the emissions of other carbon-intensive industries like semiconductor manufacturing and forestry and paper products 1. The calculation of emissions from Scope 1 and 2 (i.e., emissions from direct on-site and indirect purchased energy) shows that the global pharmaceutical sector is 55% more greenhouse gas intensive than the automotive sector 2. This means that cars, vilified for their global warming potential, are greener than medicines when it comes to manufacturing.
The pharmaceutical industry will need more life science professionals—from facility designers to pharmaceutical engineers—to address the impact of the industry’s internal manufacturing operations. These operations will be a crucial lever for contributing to the carbon savings that most pharmaceutical and biotechnology companies have committed to deliver (see Figure 1).
The industry has a unique opportunity to examine its own direct manufacturing impact. In doing so, it may uncover legacy, carbon-intensive operations that can be replaced with technologies that deliver the same consistent regulatory compliance and microbiological safety assurances with higher energy efficiency and using more clean energy sources for improved environmental performance.
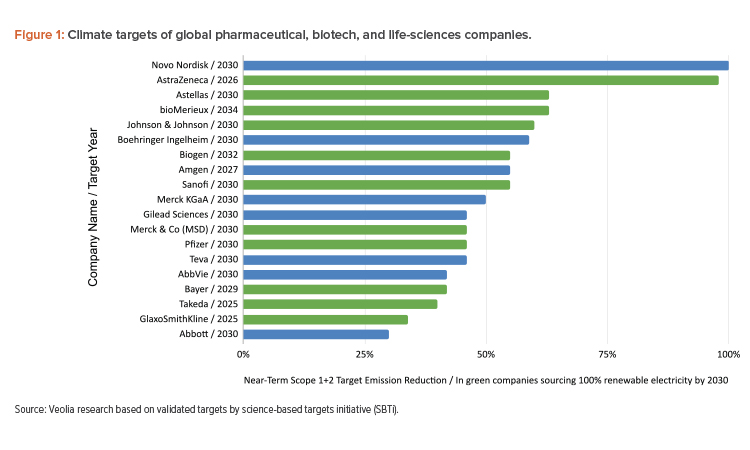
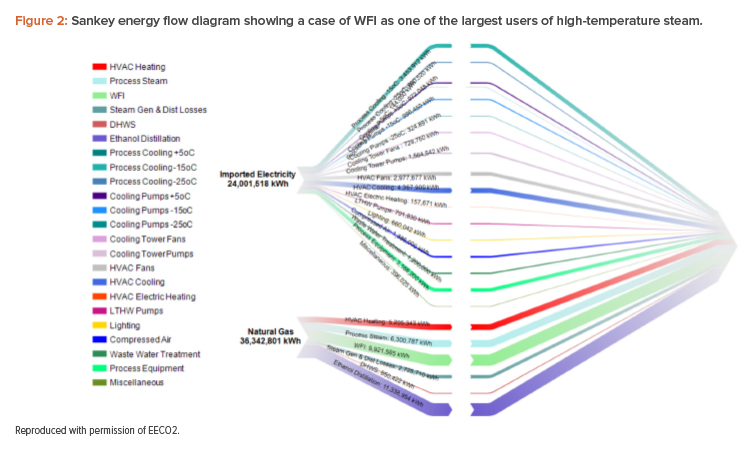
What Is the Purpose of WFI?
WFI, obtained through a further purification of pharmaceutical purified water, has the highest purity and sterility. It also has one of the largest carbon footprints associated with drug manufacturing and bioprocessing. WFI has played a critical role over time in enabling a multitude of core pharmaceutical processes—from the preparation of irrigation solutions to the production of small-molecule active pharmaceutical ingredients (APIs) used in parenteral medicines.
Beyond these traditional uses, WFI has also become an essential commodity in the making of biological drugs derived from cells cultured in bioreactors, biotechnology research, and biomanufacturing. It can also be used for contaminant-sensitive biological needs, such as rinsing for cleaning production vessels and equipment, diluting buffers for chromatographic purification, hydrating dry powder media for growing microorganisms, and preparing solutions for actual products for injection, such as vaccines and advanced therapy medicinal products.
Rapid advances in biomanufacturing with tight specifications for microbiological purity and the absence of endotoxins have exposed the need to provide greater volumes of WFI, an essential commodity that is as critical to biomanufacturing as it is to its decarbonization plans. The need for generating larger volumes of WFI, boosted by the pandemic-driven race to produce COVID-19 vaccines, has made it the biggest driver of critical utility usage—and therefore energy input, spending, and emissions.
WFI Carbon Emissions
Energy mapping, the visual representation of energy demands within a facility, shows that it would be most advantageous to curb the largest energy loads. For critical utilities, it means first reducing WFI demands. After all, WFI should only be used in those applications for which it cannot be replaced with a lower-emission substitute, such as purified water. But this step alone is not enough.
For the longest time, WFI generation has been dominated by long-lived, capital-intensive distillation equipment that uses a lot of energy in the form of thermal heat produced by fuel-fired, combustion-based systems, called stills (see Figure 2). Stills, which produce large amounts of emissions, cannot be easily decarbonized. Since their introduction in the 1970s, stills have become so pervasive and energy intensive that they are now the top contributor to clean utility emissions and, thus, a key obstacle to achieving substantial carbon savings.
Solutions that include cold and ambient temperature could easily supply the majority of global WFI needs once regulators and industry embrace greener technology that aligns with carbon emission reduction goals and cost savings.
The high-energy intensity of “steam machines”3 is, unfortunately, hardly surprising. By essentially boiling large amounts of water, distillation relies on the transfer of massive amounts of thermal energy input (i.e., process steam) to vaporize the feed water and achieve the phase transition from water to steam. Thus, the key to the purity of WFI is in this phase change that ensures that particles, endotoxins, pyrogens, and other contaminants are not carried along during the subsequent condensation and cooling steps.
Multiple-effect (ME) distillation, the most expensive and carbon-intensive WFI production technique despite all its advances in heat recovery, surprisingly remains the most dominant WFI purification method globally. Vapor compression (VC), an electrically assisted distillation technology with much lower steam demands, is less carbon intensive. VC and ME distillation account for at least one-fifth of on-site combustion-related emissions and at least one-tenth of average total energy demand4.
Why Is Reform Now Possible?
Distillation did not become the exclusive form of WFI purification by accident. Following decades-old requirements, regulators in charge of safeguarding the sterility in diagnostic, therapeutic, and parenteral drug products had restricted WFI production to heat-based distillation. Regulators still believed that only heat-based distillation with a phase change could guarantee absolute chemical and biological quality. For pharmaceutical products to be traded internationally, they had to be produced in facilities generating hot WFI, the method in accordance with most international pharmacopeias. This made alternative means of WFI production difficult and fraught with risks.
The development of current distillation methodology reveals why the shift from hot to cold WFI production is inevitable. First, regulators are not running behind anymore. They have caught up with technology, energy conservation, and decarbonization needs. Since 2017, all national pharmacopeias except for Chinese pharmacopeias have allowed global drug and therapy makers to produce WFI using purification methods other than distillation5.
Second, technology providers have the energy-efficient solutions needed to address the challenges of water purification without high-temperature heat and the emissions derived from fossil fuel combustion. Third, regulation is aligning with the need for renewable energy deployment, and market economics also point toward a carbon-constrained future with higher carbon taxation and lower electricity costs due to the rapid decarbonization of on-site energy sources6 and national electricity grids. This has contributed to a shift in WFI production from natural gas–fired steam boilers to greener all-electric WFI systems at ambient temperature.
Cold WFI membrane systems, a greener technology that has yet to be fully adopted, are estimated to meet no more than one-fifth of the new WFI needs7. Solutions that include cold and ambient temperature could easily supply the majority of global WFI needs once regulators and industry embrace greener technology that aligns with carbon emission reduction goals and cost savings. Hot WFI could be phased out considering the following:
- The efficiency of stills is unlikely to significantly improve as the industry has pushed their operational limits for decades making them, more likely than not, as efficient as they can possibly be.
- Steam generation has gained productivity over time through waste heat recovery and condensate return. But soaring fossil fuel prices and the potential for carbon taxes also increase the costs of steam-heated distillation.
- The adoption of large electric boilers that could decarbonize steam generation is hindered by much higher operating costs compared to those of fossil fuel–fired boilers, as the weighted average electricity price is almost four times higher than the average price of natural gas for the same unit (joule or kilowatt equivalent) of energy.
These points, along with the pressures of the environmental, social, and governance (ESG)8 movement driving net-zero strategies, are reinvigorating the way companies approach decision-making around the energy-related emissions of WFI generation assets—80% of which rely on steam produced by the combustion of fossil fuels, either natural gas or other hydrocarbons7.
Cold WFI Systems: Reverse Osmosis
Reverse osmosis (RO), a process that rejects ions using an applied pressure to force water through a semipermeable membrane, introduces reduced energy costs compared to thermal techniques. Unlike steam-heated distillation, RO is a physical process that involves neither high temperatures nor phase changes. Thus, it became known as cold, or ambient, WFI when followed by an additional downstream module and membrane barrier to produce pharmaceutical water of the highest purity and sterility.
Engineers and critical utility managers unfamiliar with cold WFI systems may ask whether membrane systems are new and, therefore, risky. They are neither. RO has long been the technology of choice for demanding applications such as ultra-pure water production for semiconductor manufacturing. In the pharmaceutical industry, membranes have produced US Pharmacopoeia and European Pharmacopoeia Purified Water and the now-defunct European Pharmacopoeia Highly Purified Water grades since the mid-1980s and early 2000s, respectively.
Since then, RO cleaning operation procedures have been perfected with sanitary construction, advances in hygienic system design, and the emergence of temperature-resistant polyamide material. This has enabled the use of hot water sanitization to inactivate microbes and control fouling and biofilm formation without the addition of chemical agents.
Compared to hot systems, cold WFI consumes up to 50% less electricity than VC distillation and less than one-tenth of the overall energy use per produced volume than ME distillation9. The environmental advantages of cold WFI technology begin with the operation philosophy itself. For starters, this process converts any source of softened, dechlorinated drinking feed water into WFI through a sequential, continuous purification process. That process features electric-driven pumps and a membrane barrier integrating RO, chemical-free continuous electric deionization, and ultrafiltration.
Unlike thermal distillation, water filtration through membranes does not require generating steam or changing water phases, both very carbon-intensive processes. Instead, high-pressure pumps force the water through the membrane system, generating more modest CO2 emissions. To further reduce them, pumps are equipped with variable frequency drives. These devices adjust the membrane feed pressure to fluctuating levels of demand in real time by automatically and instantaneously controlling frequency and voltage to the motors. This saves time and electricity demands by as much as 20% while extending the system’s lifetime and avoiding costly breakdowns10.
Reducing Risks and Costs
No WFI generation system, no matter how energy efficient, will succeed if it doesn’t control microbiological risk and maximize water recovery while minimizing workforce interventions. Membrane-based generators address these challenges with new and enhanced features.
First, to meet the need for bioburden and endotoxin control derived from the higher microbial risk of operating at ambient temperatures, hot water sanitization is a safe and effective practice that also optimizes the flow through membranes by preventing scaling and fouling. The amount of energy for heating to 80°C is relatively low compared to the continuous steam demand for distillation or storage heating11, and an electric heater or heat pump powered by renewable sources can sanitize the system with hot water and zero emissions.
Second, ultra-high volumetric recovery rates minimize the water footprint, particularly in areas with water stress or tight limits on wastewater discharge permits. This is done by recirculating the RO concentrate through another stage equipped with temperature and pH control devices to reduce the wastewater volume drained by up to 50%. Third, cold WFI production, membrane cleaning, and system maintenance operations are optimized with additional monitoring and sampling hardware to control risk and performance through real-time analytics and data-driven process automation to save energy and costs.
Additional Benefits of Cold WFI
Cold WFI energy savings extend beyond the generation step. Storage tanks, designed to compensate for the peak in WFI demands, and distribution pipelines, which circulate WFI from the storage tank to the consumption points, can also be designed to eliminate the heating and cooling steps typically required for hot WFI before utilization.
The easiest way to upset the quality of WFI systems is microbial activity getting out of control, particularly bacterial growth in storage tanks and distribution loops. Operating them under hot temperatures has been a popular antidote to keep bioburden at bay. But continuous recirculating, self-sanitizing hot water systems, which today represent more than 70% of the total WFI installed capacity12, come at the cost of increasing already bloated steam-related costs and emissions.
But the problem goes beyond energy consumption. In GMP environments, most WFI applications other than cleaning—which have been all but eliminated in facilities with single-use systems—require ambient WFI, particularly when biological products suffer thermal degradation above 25–30°C13. In addition, the required cooling mechanism necessary to protect the integrity of biological processes and the safety of users is an energy guzzler and a source of endotoxin and bacterial contamination14. An additional operational efficiency of cold WFI systems is that hotter systems are associated with greater rouging and shorter longevity due to faster wear of some mechanical components.
In short, suppressing microbial proliferation through high-temperature circulation may be operationally questionable and financially and environmentally irresponsible in the face of the industry’s commitment to achieving cost-efficiencies and net-zero targets.
To eliminate thermal energy consumption while controlling bacterial potential, forward-looking utility designers also favor ambient temperature storage tanks and loops sanitized through continuous injection of ozone, which is designed to be depleted via radiation before distribution. With appropriate contact time, ozone produced either by electric discharge or electrolytically, for example, ensures WFI delivery at the temperature required for most biopharmaceutical uses. At the same time, it delivers substantial savings in capital investment as it avoids the complexity of the heating and cooling loops and the installation of multiple coolers at each point of use15. For those limited uses in which hot water is preferable, a reduced hot sub-loop operating above 65°C ensures microbial destruction while requiring smaller heat exchanging capacity.
According to the Parental Drug Association (PDA)12, only about 10% of installed systems in operation feature a low-temperature approach to WFI storage and distribution. Energy and carbon constraints, as well as cost efficiencies, may be changing that. Not surprisingly, ambient designs are growing fast. They are five to seven times less expensive and up to 80% less polluting than maintaining hot storage and distribution loops. These benefits rein-force membrane-based WFI’s long-standing price edge over distillation-based generation, an advantage that is even greater with an end-to-end cold WFI solution in which the making, storage, circulation, and usage are all at the same ambient temperature.
Energy Transition to WFI Transition
Aside from regulatory drivers, the emergence of membranes for WFI is an unintended consequence of the convergence of two forces: the ambition to reach net-zero emissions and economic factors. As the industry pushes toward a decarbonization of distributed technologies, such as energy storage and microgrids, the need for all-electric cold WFI generation makes membrane technology a plausible solution to meet zero-emission targets.
However, economic pressure is equally effective at driving the transition to cold WFI. For engineers and managers of clean utilities, switching to cold WFI helps them do more with less: delivering the same consistent WFI quality inside the loop and at the point of use with higher energy savings and lower utility costs. At the same time, they take on a modestly higher level of microbiological risk. These risks, which can be efficiently managed through a holistic process and quality control strategy, are handsomely rewarded. The trade-off allows facilities to move closer to net-zero targets, reduce grid reliance, eliminate exposure to fuel price volatility, stabilize energy costs, and boost resiliency and energy security.
Electrified WFI Improves Clean Power Generation
When paired with expanding renewable energy sources, electrified cold WFI systems allow facilities to become closer to eliminating carbon emissions altogether. This unique proposition leverages the pledges of many global pharmaceutical and biotechnology companies to run 100% of their plants on a fully decarbonized electricity supply. Their investments—either through purchasing from adjacent off-site renewable sources or by integrating on-site demand management, storage, microgrid, and distributed solar generation6—are important in significantly lowering electricity costs. This is a key to the competitiveness of electrified solutions along with the implementation of carbon pricing, a practice already adopted by many pharmaceutical giants to shape their future investment decisions3.
Just as pure water decarbonization impacts clean energy production, membrane-based technologies will also be impacted by future carbon-neutral building codes for industrial plants in the US and Europe17, 18. These codes will help ensure a very high-energy performance and zero on-site combustion emissions. This union of net-zero building standards, ultra-efficient pure water systems, and clean electricity solutions will be at the core of corporate climate strategies.
Getting Started with Low-Carbon WFI
As demonstrated by the differences between hot and cold WFI, it is unequivocal that membrane systems are a clear short-term answer to the current energy crisis. They are natural candidates for installation during capacity expansions and newly constructed energy-efficient facilities. However, this alone will not be enough. As we look to a net-zero future in which all facilities are part of this effort to transition to clean-powered cold WFI technology, the top-of-mind question is “where to start and how can we pay for it?” After all, unless modern, electrified replacements for hot WFI are chosen, we will continue to need difficult-to-decarbonize steam heating, making net-zero goals more difficult to reach.
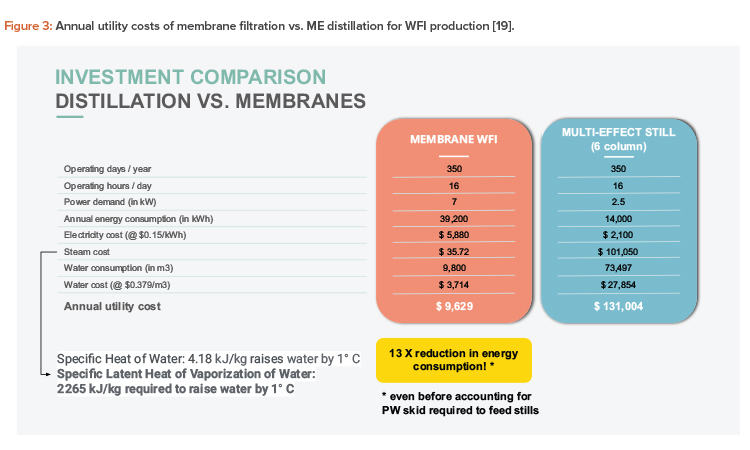
The first step is to focus on the retrofit of WFI systems that are outdated but not old enough for replacement. It’s unlikely that manufacturers will replace high-cost purification equipment unless it’s nearing the end of its lifespan, which for distillation units can be up to 20 years17. For plants that can afford the capital expense, the installed costs for cold WFI relative to potential savings on energy spending (e.g., when switching from hot to cold WFI) often mean that membrane systems are less expensive within periods as short as four years, thanks to their much higher energy performance, which offsets the upfront cost over time. The payback period shortens considerably if integrating lower clean energy costs and higher carbon taxes.
Short of making the outright investment in cold WFI equipment, one way for facilities to make WFI retrofits financially attractive to the balance sheet is by leveraging budget-neutral strategies. With this type of strategy, a portion of the savings of eliminating steam demand are diverted from the existing utility budget to finance a loan that pays for the WFI system upgrade. Under this plan, facilities take advantage of reduced operational spending, no upfront capital outlays, and full ownership of the equipment, which continues to accumulate energy savings that compensate for the cost of the retrofit after the loan repayment.
Another alternative is a model known as Water-as-a-Service. This is as a pay-per-use program that allows facilities to benefit from on-site cold WFI production with uptime guarantees and without upfront investments while offloading responsibility for maintenance schedules, operational risks, and regulatory compliance onto the equipment supplier and service provider.
Cold WFIMakes Good Business Sense
Because of tighter margins and growing competitive pressures, the industry has been driving manufacturing cost-efficiency for years. With surging energy costs, modernizing WFI production is far from the only initiative to rein in spending and emissions, but it is a quick win that can deliver significant reductions in critical utility emissions.
The recent rise in energy costs may have been a blow for pharmaceutical engineers mulling over ways to limit utility expenses. Instead, it should be a wake-up call to provide equipment vendors with clear energy use guidance through user requirement specifications that help them achieve optimized equipment designs. As long-lived, energy-intensive assets are locking future costs and emissions for 20–30 years, we should all think long and hard about how the impact of our decisions may contribute to higher, not lower, emissions in the future. To be sure, net-zero targets can’t afford the installation of new stills that rely on boilers burning fossil fuels until mid-century.
The efficient, electric solutions to break free from legacy WFI technology are affordable. And their economic benefits are also inarguable. From a capital expense perspective, they are up to 43% cheaper than equivalent stills, which take a higher level of pretreatment and thus, have a larger carbon and physical footprint. From an operational point of view, the savings can be even larger depending on system capacity, utility costs, etc.
Optimizing for the smallest energy, carbon, and physical footprint isn’t just a win for the environment. It is good for business too, with clear operational and financial benefits. Other valued business benefits—such as enhanced reputation, goodwill, and trusted relationships with employees, consumers, and investors who track the progress of companies through rating systems such as Carbon Disclosure Project and Global Real Estate Sustainability Benchmark—may be more intangible but are just as critical.
What Will a Transition Accomplish?
Ultimately, the choice between cold and hot WFI systems for drug makers becomes a decision about costs. The difference lies in when, how much, and how often they will pay. Although the annual costs of inaction are not visible, they do accumulate for the planet and the bottom line. The longer pharmaceutical and biotechnology companies wait to mitigate energy price volatility, the greater their climate, insurance, market, credit, and, above all, reputational risk become. Planning and managing a climate-resilient future has become essential. Companies either act on the transformations they committed to or risk stakeholders forcing those transformations upon them. Consumers, investors, regulators, and employees are all calling for more accountability from companies when it comes to adopting sustainable manufacturing practices.
Conclusion
From the industry’s earliest days, and especially throughout the pandemic, pharma professionals have been at the forefront of science, advancing our understanding of disease, developing new and innovative treatments, and moving those treatments into production at warp speed.
Our best shot for delivering on the pledge to reach net-zero emissions is to use the same exceptional strengths that brought the scientific, industrial, and logistical achievements that culminated with the swift deployment of multiple effective COVID-19 vaccines and therapies—catalyzing the hope of billions of people around the world. Membrane-based systems offer a ready starting point for safer, cleaner, leaner WFI generation. It’s time to turn the tide and muster the same passion, purpose, and urgency to propel the decarbonization journey ahead of us.
United again around the net-zero goal, pharmaceutical engineers should build on the same resolve and immediate response that helped the world through the pandemic. To be sure, it will not be easy. The size, speed, and scope of the change can be daunting as processes and technology aren’t typically replaced on a dime. But we need not wait three decades to start. The sooner a proactive transformation of critical utilities starts, the better the chances of succeeding before 2050 and avoiding a more reactive, more expensive energy transition.