Remote Observation Technologies in the Pharmaceutical Manufacturing Space
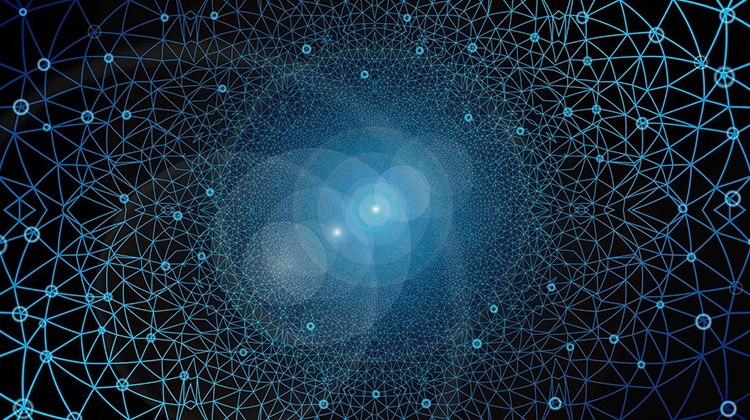
Contemporary communications technologies, particularly those relating to the internet, have the potential to revolutionize pharmaceutical manufacturing practices. The judicious use of network communication tools may benefit manufacturing operations in a number of different ways.
1 Introduction
Contemporary communications technologies, particularly those relating to the internet, have the potential to revolutionize pharmaceutical manufacturing practices. The judicious use of network communication tools may benefit manufacturing operations in a number of different ways. For example, mobile communications tools adapted for cleanroom use will empower remotely-located subject matter experts to assist staff on the factory floor in both training and troubleshooting. Remote access to real-time manufacturing system data can expedite maintenance procedures and has led to analytical tools (both local and cloud-based) appearing on the market for automated, preventive maintenance solutions. Network video products will compliment all these efforts; cameras embedded inside critical manufacturing processes can stream live video for use by staff located anywhere on a company’s global network. Some companies are embracing all of these concepts. This opinion piece is intended to explore these applications and how they relate to the pharmaceutical industry.
2 The Business Case for Pharmaceutical Manufacturing Connectivity
The pharmaceutical business is becoming increasingly global, with many established companies looking to expand into emerging geographical markets. In some cases, local policies and logistical considerations may require products to be manufactured within that territory. Inevitably this model predicts a proliferation in the number of manufacturing sites that larger firms will be required to operate. This may lead to smaller, localized manufacturing sites managed using an economically-appropriate workforce, which may deny them the full suite of engineering talent afforded to larger, global manufacturing sites.
By properly using network-based communication technologies, companies can better share their global expertise with these smaller operations. This approach offers business advantages in areas such as travel and productivity. First, international travel constitutes a major cost for global business. Improved communications tools can be correlated directly to a reduction in travel spending. Second, real-time network communications can expedite technical resolutions and reduce system downtime. Of course, these business arguments are not new. Nevertheless, contemporary and emerging virtual-presence solutions, particularly in the wearable technology space, have the potential to make international network-based collaboration more effective than ever.
Video communication does not have to be limited to peer-to-peer communication between staff members. Companies have begun integrating network cameras into manufacturing systems. In addition to the benefits outlined, cameras integrated onto the line can serve to elucidate areas within the system that may be hard to see or access during normal operation. The primary driver is to have live, streaming video available for supporting staff during maintenance and troubleshooting procedures. As an extension, however, there is the potential for using temporarily-stored video streams to retrospectively analyze and investigate adverse events. The compliance implications of this concept are discussed below.
As a corollary, all of these models can also be applied to the relationship between manufacturer and system vendor. Generally speaking, through an appropriate network security policy, companies could temporarily connect system vendors to machines hosted on the company’s network, thereby allowing direct support from the system experts.
3 Camera Architecture – Separate and Distinct Room Control Logic
The concept of cameras embedded within a manufacturing system is nothing new – industrial cameras have been used as critical components in pharmaceutical lines for decades. Generally, these cameras, especially “smart” cameras, are qualified, validated measurement devices, fully integrated into the machine’s control logic.
In this article we are proposing a wholly separate camera application. The network-enabled streaming cameras operate in complete isolation from the system architecture. Since they do not contribute to product inspection and any pass/fail decision, there is no intrinsic need for such devices to be fully validated and compliant. The proposal is that such cameras would be used only to provide operational information and not for any product quality-related decision.
Figure 1. The remote visualization camera system network connectivity is implemented on the business network, and completely segregated from the automation, which resides on the manufacturing network.
Figure 2. A) Camera mounted outside of a fill line isolator. B) drawing showing camera coverage from 11 locations. C) An Axis P1214 network camera used for this application. D) Stainless steel VPHP-compliant housing provided by system vendor inside the isolator. The caustic environment and airflow considerations inside the isolator drove to the selection of a small format camera with a low thermal footprint. Images used with permission from Bausch+Ströbel, www.bausch-stroebel.com/en, and SKAN AG, www.skan.ch/en/.
4 Compliant Data Handling and Storage
In addition to live streaming to relevant employees across a company’s global network, embedded cameras present another opportunity with respect to data storage considerations. Long-term data storage is for the most part not pragmatic when costs are considered; however short-term data storage, perhaps over a matter of days, is eminently feasible. In a manner very similar to contemporary dashboard camera solutions for road vehicles, video could be stored for a short time in an effort to capture adverse events, particularly equipment malfunctions. This could assist enormously in subsequent root-cause investigations, especially if the video coverage of a given line is suitably comprehensive.
FDA 21 CFR Part 11 1 compliant video storage solutions are technically feasible; however, if the video is intended only for system troubleshooting and is not used for drug product lot release, we believe such a solution can be implemented without being considered an integral part of the validated production platform.
Figure 3. Camera technology, once integrated into the line, can be leveraged in a phased approach. This allows real-time usage of the system while considerations around (for example) GMP video data storage and potential regulatory concerns are addressed.
Figure 4. Video data storage can be devolved to a secondary phase if compliant data storage is a concern.
5 Challenges in the Pharmaceutical Manufacturing Space
The technologies discussed in this document are readily available and in some cases have traction in other major industrial markets. The pharmaceutical industry has some unique challenges that need to be met. These may be further compounded by legal considerations associated with the jurisdiction of a particular manufacturing location.
First, pharmaceutical manufacturing generally requires the use of cleanroom manufacturing protocols. Mobile peer-to-peer communication solutions must reside permanently within the clean space. The requirements of the cleanroom place constraints on the design and materials used in the construction of an approved device. The high density of piping and supporting utilities in a typical plant generally diminishes cellular reception, forcing the need for an effective local wireless network.
Real-time monitoring and visualization of factory system data is growing in importance, with several new monitoring and reporting platforms emerging in recent years from a variety of vendors. In the past, “islands of automation,’” monolithic manufacturing systems largely isolated from the internet and controlled solely through local Human Machine Interfaces (HMIs), were the standard across the industry. With the advent of the Internet of Things (IoT), we can benefit from leveraging the explosion of cloud-based industrial diagnostic tools. Connecting systems to the internet inherently introduces data security risks that must be mitigated through the diligent application of appropriate security policies and architecture.
Network cameras, if broadcast globally across a company’s network, are subject to network considerations. High performance cameras represent a challenge in terms of pragmatic bandwidth consumption. In reality, network video solutions require modest video resolutions and substantial video compression in order to achieve a viable real-time viewing experience over long distances.
In some jurisdictions the use of cameras in the manufacturing space, whether mobile or embedded into production equipment, can conflict with local employment laws. Proper implementation of camera-based technologies must consider local legislation.
Regulatory considerations in this space present a challenge, especially with regard to short- or long-term video data storage, as well as potential uses of that data. Here we propose that video data can be retained in the short term to assist with qualification and maintenance of systems without complicating normal GMP use of the machine.
Figure 5. This image shows the overall architecture used at one company. A server, separate and distinct from the manufacturing system, is used to manage all of the camera feeds. Software on the server controls user access and also allows optional, programmable video data storage capability.
6 Conclusion
Emerging network-based video solutions have the potential to improve operations in the pharmaceutical manufacturing space. With that said, the industry needs guidance from regulatory authorities to ensure that these technologies are implemented in a manner that does not compromise the viability of otherwise compliant manufacturing lines. It is our hope that this article stimulates discussion and stimulates discussion with a view to the clarification of regulatory expectations.
Limitation of Liability
In no event shall ISPE or any of its affiliates, or the officers, directors, employees, members, or agents of each of them, or the authors, be liable for any damages of any kind, including without limitation any special, incidental, indirect, or consequential damages, whether or not advised of the possibility of such damages, and on any theory of liability whatsoever, arising out of or in connection with the use of this information.
© 2018 ISPE. All rights reserved.
All rights reserved. No part of this document may be reproduced or copied in any form or by any means – graphic, electronic, or mechanical, including photocopying, taping, or information storage and retrieval systems – without written permission of ISPE.
All trademarks used are acknowledged.
Acknowledgements
This Concept Paper represents industry best practices based on the experiences and input from the individuals listed below and does not reflect the views of any one individual or company.
Document Authors
Nick Haycocks, Amgen Inc., USA
Graham Milne, Amgen Inc., USA
Particular thanks go to the following for their support and review of this Concept Paper: Murugan Govindasamy, (Pfizer Inc.), Rob Miller (Pfizer Inc.), and members of the ISPE Guidance Documents Committee (GDC).
Comments on this paper may be sent to: haycocks@amgen.com.